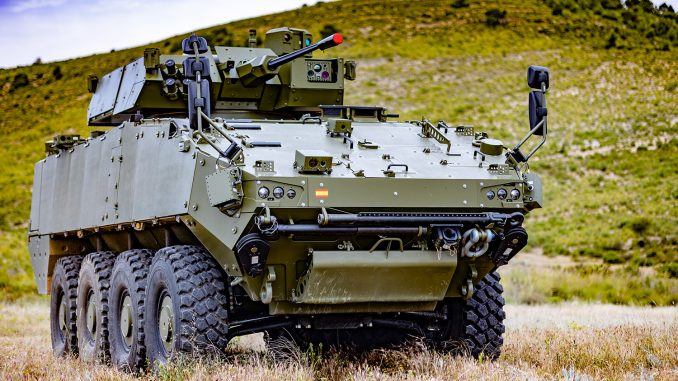
Désormais, tous nos lecteurs savent ce qu’englobe le concept de « maintenance prédictive » et quels avantages elle offre par rapport à la maintenance traditionnelle ou réactive. L'entreprise espagnole EM&E (Escribano Mechanical & Engineering) entend aller plus loin avec ses stations d'armes, en ajoutant à cela un apprentissage et une supervision intégrés, qui permettront aux personnes chargées d'effectuer la maintenance et les réparations de premier et deuxième échelons de pouvoir effectuer des tâches. jusqu'ici réservé aux échelons supérieurs. Un projet initié sur proposition du MALE (Army Logistics Support Command) et dont la réussite sera clé pour le futur Bureau d'Appui Technique du Cycle de Vie (OTACV) du Programme VCR 8×8.
Pendant la guerre froide, la présence de dizaines de milliers de chars du Pacte de Varsovie constituait l’une des principales menaces auxquelles étaient confrontés les États membres de l’OTAN. On pourrait en dire autant des forces aériennes de l’Est et de leurs marines, compte tenu du grand nombre de plates-formes qu’elles maintenaient en service. Pour contrer ces menaces, et sachant qu’il était impossible d’égaler en quantité les Soviétiques et leurs alliés, la technologie a été choisie comme moyen de surmonter une écrasante infériorité numérique. De cette façon, La conception des véhicules blindés (et d’autres plates-formes, armes et systèmes d’armes) est devenue de plus en plus sophistiquée., intégrant de meilleures directions de tir, des moteurs de plus grande puissance, des transmissions complexes et un grand nombre d'équipements électroniques.
Maintenir un plus petit nombre de plates-formes en service - sans chercher à ignorer les avantages que procurent les technologies à la merci de la Deuxième Stratégie de Rémunération prévue– a toujours entraîné une moindre résistance à l’attrition. En d’autres termes, en cas d’affrontement, chaque perte, qu’il s’agisse d’une perte au combat ou d’une rupture impossible à résoudre sur le terrain, se ferait bien plus sentir dans les rangs occidentaux que dans les rangs soviétiques.
maintenance prédictive, comme nous l'avons expliqué il y a quelques mois, découle de la nécessité de maintenir une grande opérabilité dans des médias qui, en raison de leur coût et de leur nombre relativement restreint, n'étaient pas - et ne sont pas - superflus. Contrairement aux Soviétiques, pour qui les moteurs d'aviation ou les hélices de leurs chars de combat étaient quelque chose à produire en série et, si nécessaire, à remplacer les premiers de l'échange dans le contexte d'une guerre à grande échelle, dans laquelle était garantie la supériorité numérique, en Occident, les choses étaient très différentes. Avec des chars de combat et des véhicules blindés dont le coût augmentait de façon exponentielle à mesure que chaque nouvelle génération incorporait des systèmes et des composants de plus en plus complexes, chaque perte était une perte significative. et dans certains cas, irremplaçable, que cela soit dû à une défaillance mécanique ou à une atteinte.
Cela a été clairement démontré à plusieurs reprises, comme en Irak le 19 mars 2003. Puis, opérant depuis la base saoudienne d'Arar, une colonne de 718 millions de véhicules Pinzgauer Il s’est rendu au cœur de ce pays du Moyen-Orient avec pour mission de créer le chaos derrière les lignes ennemies. Aux commandes se trouvait le lieutenant-colonel Pete Blaber, dont nous avons d'ailleurs parlé dans l'article sur le Opération Anaconda. Blaber et ses hommes, après avoir parcouru six cents kilomètres, ont dû prendre le contrôle du barrage de Haditha - à environ 300 kilomètres à l'ouest de Bagdad - pour empêcher les Irakiens de le détruire et d'inonder les routes approchant de la capitale irakienne par le sud, qui était l'axe de la principale avancée américaine.
Après avoir pris l'objectif avec l'aide du 75th Ranger Regiment, ils devaient passer à la deuxième partie de la mission, qui consistait à simuler une offensive alliée depuis le flanc ouest qui allait semer la confusion parmi les commandants irakiens. Pour crédibiliser l'attaque, le 24 mars, la base aérienne H1 est capturée intacte et une douzaine de M1 sont transportés. Abrams sur plusieurs C-17A Globemaster modifié pour USSOCOM. Avançant avec pratiquement aucun soutien logistique, en moins de deux semaines de combats contre plus de la moitié du M1 Abrams Ils étaient inopérants, la plupart à cause de pannes, à l'exception d'un qui s'est renversé dans un fossé et a dû être abandonné (après autodestruction pour éviter de tomber aux mains de l'ennemi). C'est-à-dire qu'en 15 jours d'opérations, et sans avoir subi une seule perte due à l'impact d'une grenade ou d'un missile ennemi, l'unité avait perdu la moitié de ses effectifs, réduisant d'autant sa capacité de combat.
Bien entendu, ce n’est qu’un exemple parmi des milliers possibles. En tout cas, c'est très révélateur et devrait nous faire réfléchir sur ce qui arriverait dans des opérations plus longues et à une armée qui n'aurait pas les moyens de l'armée américaine, car si cette dernière s'est toujours distinguée par quelque chose, c'est par sa capacité logistique et sa forte proportion entre le nombre de personnels en uniforme à l'arrière et ceux affectés au front.
À cela, il faut ajouter un deuxième facteur, à savoir que la complexité des systèmes d'armes actuels multiplie le nombre d'erreurs possibles, notamment celles liées aux composants non mécaniques, tels que les logiciels ou l'électronique. Dans ce sens, un véhicule comme le futur VCR 8×8 Dragon Il pourrait devenir inutilisable au combat non seulement parce que le moteur ou la boîte de vitesses explose, ou parce que plusieurs pneus se dégonflent, parce que son arme principale se coince ou toute autre chose que nous pouvons imaginer. Il pourrait également devenir inopérant si le logiciel de gestion du champ de bataille, ou le logiciel qui contrôle la station d'armes, « se bloque » pour une raison quelconque ou si l'un des nombreux processeurs qu'ils intègrent tombe en panne.
Logiquement, plus le nombre de sous-systèmes est élevé, plus il y a de chances qu'un tel phénomène se produise et que ni l'équipage ni les équipes de maintenance les plus proches du front ne puissent rien faire pour le résoudre. Du moins pas sans pouvoir accéder aux connaissances d'experts sur place et sans disposer de toute la documentation et des instructions nécessaires pour mener à bien votre tâche, aussi complexe soit-elle, en tout lieu et dans toutes les conditions.
Rafael López Mercado a déclaré dans son article dédié à la maintenance prédictive que "aux États-Unis, grâce à une mentalité ouverte au changement, qui les rend capables d'assimiler les leçons apprises et de mettre en œuvre les solutions découvertes, la mise en œuvre de la maintenance prédictive a été promue dans toutes les branches de leurs forces militaires". C’est ni plus ni moins la tâche qui attend notre armée. Certaines mesures ont déjà commencé à être prises et seront importantes pour la « Force 35 ». D’autres seront plus difficiles à mettre en œuvre, mais cela ne signifie pas que nous pouvons ignorer le défi qu’ils posent.
Dans le cas dont nous discutons aujourd'hui, impliquant les stations d'armes EM&E, comme le Guardian 30 dont nous avons déjà parlé, entendent aller au-delà de la maintenance prédictive, pleinement assimilée dès les premières étapes de conception et pour laquelle ils ont intégré de nombreux capteurs dans leurs tours. Son idée est d'héberger la documentation technique nécessaire dans le cloud, de combiner maintenance prédictive et apprentissage interactif avec la réalité augmentée, d'exploiter Big Data et, en bref, trouver le moyen de garantir que, quoi qu'il arrive, ses tours continuent de fonctionner. Voyons comment.
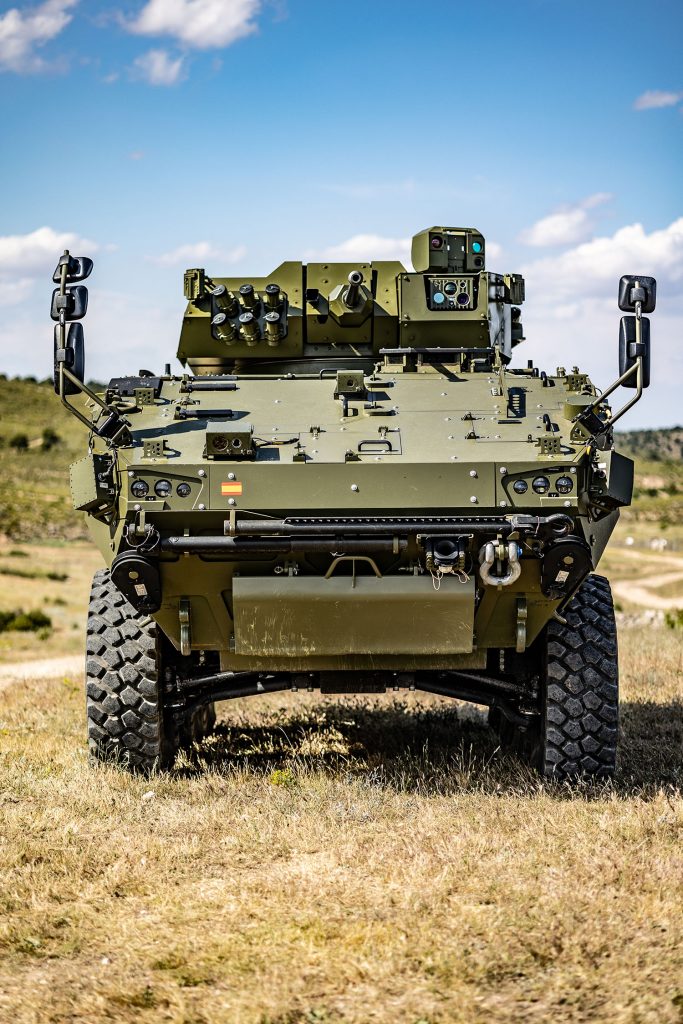
Apprentissage interactif et maintenance prédictive dans le monde civil
L’une des caractéristiques de l’époque dans laquelle nous vivons est que, contrairement à d’autres époques du passé, l’industrie civile est en avance sur l’industrie militaire à bien des égards. De nombreuses entreprises ont mis en œuvre des systèmes de réalité augmentée et d'apprentissage interactif dans lesquels, grâce à l'utilisation de lunettes VR et de codes QR ou de systèmes d'identification naturelle qui détectent les mains de l'utilisateur et les formes de ce qui se trouve devant lui, elles permettent de formez vos opérateurs.
Dans le meilleur des cas, ces systèmes permettent au stagiaire d'explorer par lui-même les parties du système sur lesquelles il doit être instruit, de pouvoir les déplacer dans pratiquement toutes les directions, d'accéder à la documentation technique, etc. Logiquement, pendant que le processus de formation est en cours, tout cela se fait sous surveillance humaine, puisqu'il est toujours nécessaire d'avoir les conseils ou les directives de quelqu'un qui connaît en profondeur le système. Désormais, étant donné la possibilité de visualiser en temps réel sur un autre écran la même chose que les lunettes VR montrent aux yeux de l'étudiant, rien n'oblige l'expert à se trouver physiquement sur le lieu où est dispensé le cours.
Ce système a ses avantages, surtout dans un monde globalisé et interconnecté dans lequel, pour citer un exemple, très peu de pays produisent des machines-outils avancées. Imaginons le cas d'une entreprise espagnole, japonaise ou allemande qui parvient à exporter aux États-Unis un système de fraisage de pointe. Ce système, installé dans une usine du Missouri, et comme le lecteur le comprendra, est d'autant plus rentable qu'il est en opération longtemps. Si en cas de panne l'entreprise de production est obligée d'y transférer du personnel (ce qui n'est pas du tout déraisonnable, mais plutôt courant), il faudra des jours dans le meilleur des cas avant qu'elle puisse reprendre ses activités.
Les options dans ces cas ont toujours été limitées. L'une, très basique et très demandée, consiste à installer une filiale dans le pays vers lequel les machines sont exportées, garantissant une maintenance 24h/7 et XNUMXj/XNUMX. Or, il s'agit d'une solution coûteuse qui non seulement réduit la marge bénéficiaire de l'entreprise exportatrice, mais qui pose aussi souvent des problèmes en dépendant davantage des sous-traitants que des techniciens provenant effectivement de la société mère, puisque celle-ci peut rarement se passer de son personnel pour envoyer sous d'autres latitudes, et encore moins s'occuper de plusieurs incidents en même temps, au sein d'équipes réparties dans plusieurs pays. La solution est de former les opérateurs de ces machines dans leur maintenance à travers un apprentissage interactif, en réduisant au minimum les occasions dans lesquelles il est réellement nécessaire de transférer son propre personnel.
Bien entendu, rien de tout cela n’implique que le personnel local soit en mesure d’effectuer toutes les réparations possibles. Pas même toutes les tâches de maintenance que nécessitent des systèmes complexes tels que ceux décrits. Cependant, il est possible de résoudre un grand nombre d'incidents, surtout si à la disposition de l'opérateur sur le terrain nous disposons d'un ingénieur de l'entreprise manufacturière qui, via la télématique, peut superviser les actions à entreprendre, faire des recommandations, guider le processus, résoudre les doutes, les revers, etc. On pourrait affirmer que cette façon de fonctionner n'est rien d'autre qu'une astuce des constructeurs pour réduire les coûts, mais la vérité est que c'est un système qui fonctionne, de plus en plus demandé et qui répond à l'objectif ultime : faire fonctionner ces machines pendant toute la durée de leur fonctionnement. temps, autant de temps que possible.
En passant du monde civil au monde militaire, on constate qu'il n'y a pratiquement aucune différence entre les machines que nous avons utilisées comme exemples (fraiseuses, découpeuses, imprimantes 3D, grands tours, estampeuses, presses...) et les armes modernes. systèmes. Si, revenant au cas du VCR 8×8 Dragon, nous regardons l'ensemble, nous verrons qu'il comporte plusieurs sous-systèmes, dont chacun peut tomber en panne, faisant perdre au véhicule sa capacité de combat ou le dégrader. Ainsi, si les systèmes optroniques tombent en panne, si le moteur en dit assez ou si l'anneau de la tour se coince ou si le moteur électrique qui le déplace tombe en panne, nous nous retrouverons avec un système d'armes aussi coûteux qu'inutile, puisqu'il pourrait pas se battre avec des garanties. .
Les conditions dans lesquelles il doit servir, tant en manœuvre qu’une fois sur le théâtre des opérations, étant particulièrement exigeantes, nous risquons continuellement des échecs de toutes sortes. Cela les rend excessivement dépendants des capacités de maintenance disponibles, notamment celles du premier et du deuxième échelon, qui sont celles qui permettent de remettre un système au combat dans les plus brefs délais. Or, cela n’est pas toujours facile, car à ces niveaux on dispose rarement des moyens ou des connaissances nécessaires à certaines tâches. C’est là que l’apprentissage interactif et la maintenance prédictive entrent en jeu.
La maintenance prédictive peut se résumer, très simplement, à la capacité d'effectuer les tâches de correction ou de remplacement nécessaires au bon fonctionnement d'un système avant qu'une panne ne survienne. D'une certaine manière, chaque fois que nous amenons la voiture au garage, remplaçons l'huile ou changeons les filtres, nous faisons la même chose. Désormais, dans les scénarios où l'enjeu n'est pas un appel à une dépanneuse ou des vacances ratées en raison d'une panne mécanique, il faut quelque chose de plus. C'est ici qu'intervient la maintenance prédictive, car elle nous permet de connaître l'état de plusieurs composants en temps réel, ce qui permet d'avancer les opérations de réparation ou de remplacement afin qu'une panne mécanique ne se produise jamais ou, du moins, qu'elle minimise les risques de panne. cela se produit.
Si l’on pense à des plates-formes complexes, comme un superpétrolier ou un porte-conteneurs, nous verrons que le personnel à bord est beaucoup plus petit que ce à quoi on pourrait s’attendre a priori, compte tenu du déplacement de ces navires. Si un monstre comme l'« Emma Maersk », d'une longueur de près de 400 mètres peut être manipulé par un peu plus d'une douzaine de personnes, ce n'est pas grâce à la magie, mais à une automatisation extrême et à une maintenance prédictive. Cela permet à la plupart des systèmes du navire d'envoyer des données sur leur état 24 heures sur XNUMX, afin qu'une personne puisse les surveiller et prendre les mesures préventives nécessaires avant qu'ils ne tombent en panne. Aussi parce qu'au fil des années, grâce à l'expérience acquise et à une meilleure compréhension des énormes quantités de données collectées par les multiples capteurs installés dans une grande flotte comme celle gérée par cette entreprise, ils savent avec certitude quelles sont les alertes de panne de chacun. composant et est beaucoup plus exquis avec les tâches de maintenance. Il en va de même pour les flottes de camions ou les flottes d’avions. Les entreprises de transport, avec des dizaines, voire des centaines de véhicules en inventaire, doivent minimiser le nombre d'incidents, c'est pourquoi elles ont développé une vaste expérience dans l'utilisation de systèmes de maintenance prédictive.
Si l’on y réfléchit, les problèmes auxquels ils doivent faire face ne sont pas très différents de ceux auxquels est confrontée une armée comme l’Espagne, avec une flotte blindée qui se compte par centaines de véhicules. Sans aller plus loin, dans le cas du futur VCR 8×8 Dragon, nous parlons de 348 unités seulement dans la première phase, qui seront construites par le consortium TESS Defence, composé de Santa Bárbara Sistemas, Indra, SAPA Placencia et Escribano. Génie mécanique.

Maintenance prédictive et Guardian 30
A la fin de la section précédente nous avons fait référence au programme VCR 8×8 Dragon de l’Armée. Comme nous le savons, ledit véhicule montera - en l'absence de résolution du recours présenté par Pap Tecnos - sur les tours Guardian 30 d'Escribano. Dans cette optique, la Direction générale de l'armement et du matériel (DGAM), responsable d'un programme qui, s'il était réalisé, serait évalué à près de 4.000 milliards d'euros, a entamé les travaux sur le cycle de vie des futurs véhicules, dont les tourelles. A cet effet, elle envisage de créer un Bureau d'Appui Technique du Cycle de Vie (OTACV), doté du personnel et des moyens nécessaires pour garantir la disponibilité opérationnelle et que les coûts de maintenance tout au long du cycle de vie ne dépassent pas les prévisions. Comme l'explique Infodefensa:
«Le bureau travaillerait dans quatre domaines principaux : l'ingénierie de maintenance, les mises à jour et modifications, la gestion avancée du maintien en puissance et des pièces de rechange et la logistique des matériaux. Leurs tâches seraient très diverses : disponibilité opérationnelle ; réglage, calibrage et alignement des équipements ; soutien aux organismes logistiques ; entretien des équipements; gestion de la maintenance prédictive ; enquête sur les défauts et identification des défauts ; contrôle et gestion de la documentation technique; contrôle de configuration ; gestion de l'obsolescence ; exploitation du jumeau numérique ; gestion des modifications et des actions sur les équipements et les systèmes ; gestion des rénovations ; fourniture de pièces de rechange et de composants ; et gestion des activités de formation.
Réaliser tout cela dépasse les capacités du MALE ou de la DGAM et sera impossible sans l'implication des entreprises qui forment le consortium chargé de la production des nouveaux véhicules, ainsi que des armes et autres systèmes qui y sont installés. Dans le cas spécifique de l'EM&E, la tâche est de mettre en œuvre cette maintenance prédictive et cet apprentissage interactif dont nous avons parlé précédemment et, de l'avis de ses ingénieurs, de les combiner pour réaliser un ensemble beaucoup plus utile aux objectifs de l'Armée. . Pour ce faire, il sera essentiel d’approfondir une série d’axes de travail, tels que :
- Améliorez les capacités d’analyse des données : créer une base de connaissances sur laquelle baser la maintenance prédictive. Comme nous l'avons dit, lorsque les tours entreront en service, nous parlerons de centaines d'unités, chacune dotée de plusieurs capteurs et toutes transmettant en temps réel. Des outils d’analyse puissants seront nécessaires pour extraire les informations réellement utiles d’un tel enchevêtrement de données.
- Implémenter des systèmes de réalité augmentée : afin que la tour puisse montrer à l'utilisateur des données précises en temps réel sur l'état ou la fonctionnalité du système, en plaçant l'information synthétique avant ce que l'œil voit grâce à l'utilisation de lunettes de réalité augmentée telles que Google Lens. Ceci, qui semble un peu énigmatique, signifie que l'entreprise doit créer une interface solide, intuitive et fonctionnelle qui permette de transformer les données produites par le système en informations utiles pour l'opérateur de maintenance, pour l'ingénieur en charge et même pour l'équipage s'il doit intervenir à la volée.
- Virtualiser les systèmes (jumeau numérique) : Les produits disposeront d'un simulateur intégré qui permettra une expérience de réalité immersive, reproduisant l'environnement physique et créant la conscience de la situation nécessaire pour que la personne chargée de superviser le système ait un accès virtuel à tous les éléments qui le composent et puisse non seulement évaluer eux, mais aussi les gérer à distance.
De la combinaison de ces trois axes de travail, ils espèrent qu’émergera un système intégré de maintenance et d’apprentissage qui présente, du moins sur papier, de multiples avantages par rapport aux formes de travail actuellement utilisées.
Par exemple, le système doit être capable d'indiquer aux échelons quand et comment les opérations de maintenance doivent être effectuées via un liste de contrôle qui permet d’établir une méthodologie de travail unique. Mieux encore, dans le cas où, pour quelque raison que ce soit, cela change (par exemple après une nouvelle analyse des données envoyées par les capteurs installés sur les tours), ladite liste de tâches serait mise à jour en temps réel dans le cloud, devenant ainsi disponible pour tous. unités et échelons impliqués.
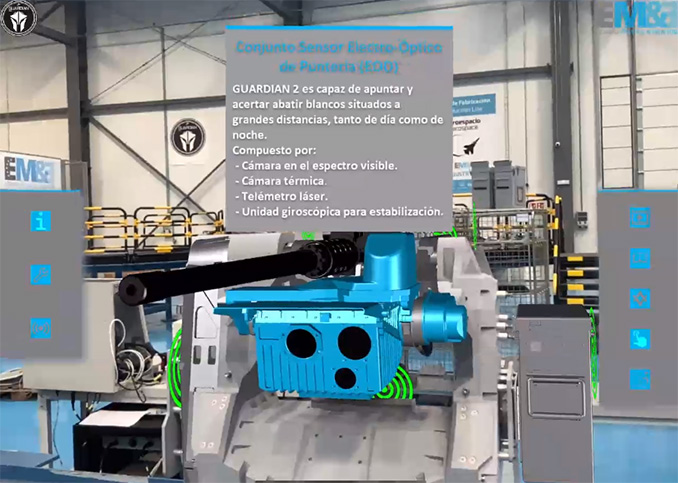
Ce dernier aspect, celui du cloud, est crucial, car ce qui permettra à terme de mettre en œuvre le modèle dans lequel travaille EM&E, c'est le développement rapide qu'ont connu les technologies de l'information et de la communication au cours des dernières années et l'accent mis sur le Les forces armées s’efforcent de s’adapter à ce phénomène. Ce sera grâce aux améliorations de la communication que les opérateurs pourront recevoir des conseils d'experts de l'entreprise elle-même s'ils en ont besoin. De plus, le moment venu, ce même expert peut prendre le contrôle du système à distance, en effectuant autant d'opérations qu'il le juge nécessaire et en accédant à toutes les informations pertinentes pour l'entretien ou la réparation. Comme l'explique l'entreprise, dans certains cas, "il est préférable qu'un de nos ingénieurs puisse voir le système avec ses propres yeux, même à distance, plutôt qu'à travers les yeux ou les impressions des autres".
Or, cette dépendance aux communications et à la possibilité d'accéder au cloud C'est aussi un talon d'Achille. Non seulement la bande passante est limitée - et elle le sera - mais les systèmes peuvent tomber en panne, les infrastructures de communication, y compris les satellites, ils peuvent être attaqués, etc. L'entreprise le sait et prévoit de disposer de systèmes de sauvegarde permettant aux opérateurs d'accéder aux informations même dans des environnements où les communications ont été dégradées.
Au-delà du goulot d’étranglement que représentent toujours les communications, il existe de nombreuses autres complications que l’EM&E tente de surmonter en investissant dans la R&D&I. L'entreprise sensorise ses produits depuis des années, ce qui, dans des cas comme celui du Guardian 30, a atteint un paroxysme, comprenant plusieurs systèmes capables de mesurer chaque donnée pertinente. Plus important encore, depuis la première phase de conception, ils ont collecté des données sur les principaux paramètres qui influencent le fonctionnement (CPU, GPU, humidité, jeux, écarts, vibrations, températures d'utilisation...). Grâce à l'analyse des données collectées, ils ont pu créer une série de bases de données constamment mises à jour, qui permettront une meilleure connaissance des besoins quotidiens de chaque station d'armement et une planification optimale de la maintenance. En somme, c’est un travail qui demandera encore des années pour offrir ses meilleurs résultats.
Pour certaines des stations que l'entreprise produit et qui ont été exportées en quantités significatives, elles disposent déjà de données suffisamment précises sur les performances et la fiabilité pour organiser la maintenance avec toutes les garanties. Dans le cas de celles livrées, par exemple, à la marine espagnole (34 tours à ce jour) ou à celle du Pérou, ce processus est toujours en cours. Concernant le Guardian 30, bien que dans ces années de conception et de tests ont pu collecter un volume d'informations important, ce sera lorsqu'ils passeront en production en série et commenceront à être installés sur les barges VCR 8×8 Dragon, qu'ils pourront disposer de toutes les données pertinentes.
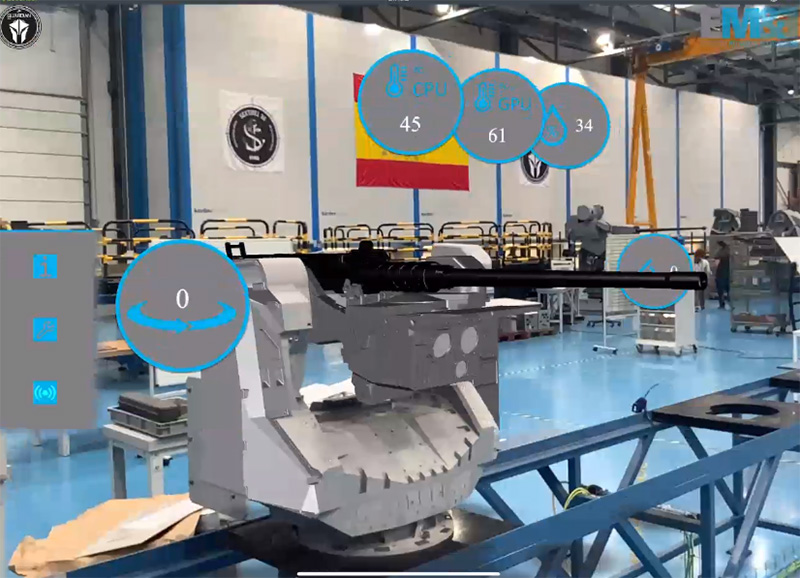
Compte tenu du nombre de capteurs par tour, du nombre de tours qui seront produites et des multiples scénarios dans lesquels ils devront fonctionner, au fil du temps, la précision des analyses deviendra de plus en plus grande, ce qui affectera positivement le cycle de vie. des postes d'armes eux-mêmes. Cependant, cela obligera l'entreprise et le bureau technique de support du cycle de vie à travailler dur sur le développement de Big Data Il est nécessaire de gérer des gigaoctets et des gigaoctets d'informations et de séparer, comme on dit, le bon grain de l'ivraie.
Avoir toutes les données mentionnées et pouvoir les analyser est un immense avantage, mais cela ne sert à rien si de l'autre côté de l'écran le personnel en charge de la maintenance n'a pas la formation adéquate ou n'a pas les ressources pour réaliser leur travail. C'est pourquoi, au-delà de la maintenance prédictive, l'entreprise considère l'apprentissage interactif et l'utilisation de ressources en ligne comme essentiels. Ainsi, les manuels d'exploitation seront inclus dans les mêmes systèmes, en plus du format papier traditionnel. L'entreprise affirme ne pas y croire, même si elle reconnaît leur importance et la nécessité pour l'utilisateur final de les connaître en profondeur. Ils soutiennent que grâce à la simulation et à la réalité augmentée, qui permettent à l'utilisateur d'apprendre à utiliser le système sans avoir besoin de manuels, de meilleurs résultats seront obtenus.
Cette façon de procéder, dans laquelle les manuels et toutes les informations techniques sont entièrement numérisés et stockés dans le cloud - avec sauvegarde dans la mémoire physique que les stations d'armes elles-mêmes incluent en cas de panne de communication -, permet aux fichiers Ils peuvent être constamment mis à jour, mais aussi que l'utilisateur puisse y accéder en toute situation, non seulement pour consultation, mais comme forme de support interactif. En fait, le défi n'est pas tant de codifier sur papier les directives de maintenance, mais plutôt de créer les tutoriels et les aides nécessaires pour que tout opérateur, avec très peu ou pas de formation spécifique sur le système en question, puisse entreprendre de multiples tâches.
D’ailleurs, même si nous prêtons pratiquement toute notre attention au matériel, la même chose peut s’appliquer aux logiciels, qui jouent un rôle de plus en plus important dans le fonctionnement des systèmes d’armes modernes. Le système nous permet de connaître combien de cycles une interruption s'est produite dans un programme et d'agir en conséquence pour le futur.
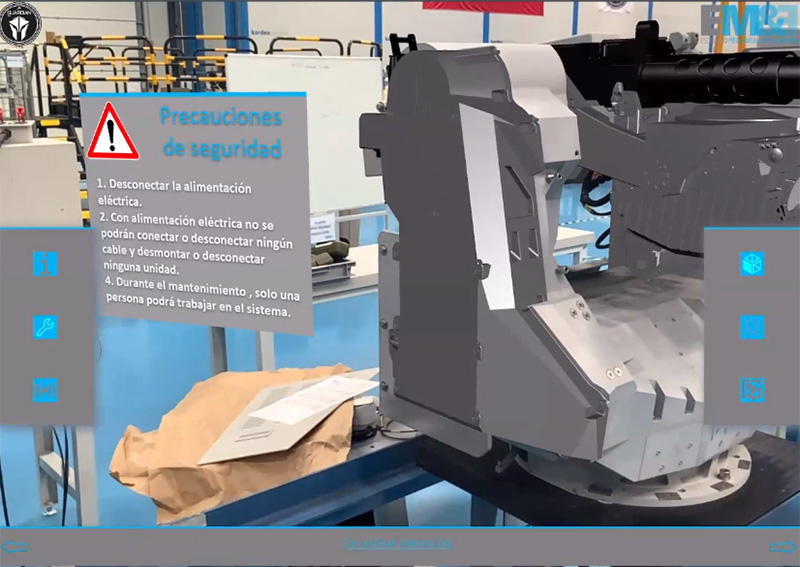
Nous avons eu l'occasion de voir le système en fonctionnement avec le directeur technologique de l'entreprise, José Carlos Hidalgo, et de vérifier, comme le montrent les images, qu'il guidait à tout moment l'utilisateur à travers chaque étape à suivre. De plus, en même temps, l'utilisateur peut consulter non seulement les données en temps réel collectées par les capteurs, mais également les caractéristiques de chaque composant. Désormais, le travail à accomplir, jusqu'à ce que chaque opération de maintenance ait son propre tutoriel PDF, avec vidéos explicatives, etc., est énorme. En fait, il faudra des années et beaucoup d’argent pour y parvenir, même si l’entreprise est déterminée à le faire à tout prix.
Selon Hidalgo, il existe également un aspect psychologique important qui maximise les avantages de cette nouvelle façon d'effectuer l'entretien : il incite les personnes chargées de l'effectuer à s'intéresser encore plus à leur travail. Cela peut sembler anodin, mais la vérité est que pouvoir « jouer » avec des composants virtuels, avoir toutes les informations à portée de main et convertir des opérations autrement routinières en quelque chose de plus amusant et intéressant, présente des avantages et contribue à impliquer le personnel dans poursuite d’un objectif commun : offrir la meilleure maintenance possible.
Enfin et surtout, il faut réaffirmer la notion de souveraineté industrielle et technologique, qui ne sera jamais telle si l'on doit faire appel à des entreprises étrangères pour assurer le support du cycle de vie. En ce sens, le fait que la barge, la tour et les multiples sous-systèmes (combat, optronique, communications...) soient espagnols permet une liberté et une indépendance totales également en matière de maintenance, ce qui ne serait pas possible de la même manière. si l'on recourait à des sociétés étrangères, même si les fameuses compensations industrielles étaient négociées et que toutes les extrémités étaient laissées sur papier. En d’autres termes, le fait que le technologue soit espagnol permet à l’utilisateur final d’effectuer toute opération de maintenance sans limitations. Malheureusement, sinon nous avons de nombreux exemples dans le FAS.

Conclusions
Les forces armées espagnoles ont longtemps privilégié la qualité plutôt que la quantité. En el caso del Ejército de Tierra y de programas como el VCR 8×8 Dragón, esta apuesta se llevará al límite, pues se trata de sistemas mucho más complejos que aquellos a los que deben sustituir, lo que limitará por fuerza el número de ellos en service. Dans ce contexte, la nécessité de maintenir chacun d’entre eux en mesure d’agir quelles que soient les circonstances est un impératif. La seule voie possible est de combiner la maintenance prédictive avec des changements profonds dans la formation et l’accompagnement des personnes chargées de réaliser ces tâches importantes. Cela implique de miser sur la réalité augmentée, la simulation, le cloud et l’analyse de gros volumes de données.
Chez Escribano, ils reconnaissent ouvertement qu'ils ne sont des pionniers dans aucune de ces technologies, mais qu'ils s'appuient plutôt sur l'expérience acquise par de nombreuses autres entreprises au cours des deux dernières décennies. Ils s'estiment désormais capables de les combiner et de développer des solutions offrant une valeur ajoutée significative afin que, par rapport à leurs stations d'armes et notamment au programme VCR 8×8, ils puissent améliorer significativement le support du cycle de vie.
Ce ne sera pas facile, car atteindre l'objectif qu'ils se sont fixé implique de sensorier chaque produit, y compris les marques naturelles ou artificielles qui permettent de montrer feuilles de données, des vidéos informatives ou des manuels, préparer ces contenus en personnalisant les informations proposées afin qu'elles s'adaptent aux besoins exacts de l'utilisateur final, simuler chaque opération de maintenance de chaque pièce, concevoir des systèmes sécurisés qui permettent de stocker les informations à la fois dans le cloud et dans les propres stations d'armes, se coordonner avec les fabricants des barges et de chacun des autres sous-systèmes qui composent un véhicule aussi complexe, etc. En bref, un défi majeur auquel ils sont confrontés en vue de pouvoir faire deux choses : 1) minimiser les possibilités de panne de leurs stations d'armes et ; 2) Si nécessaire, que les équipages ou seconds échelons disposent de toutes les ressources et du soutien nécessaires pour résoudre presque tous les problèmes sur place. Ce n'est qu'ainsi qu'ils pourront garantir une disponibilité maximale de leurs produits et ainsi garantir que les capacités de combat restent toujours élevées.
Au-delà de ce que signifie ce projet pour l'entreprise madrilène, il est évident que sa réalisation dépendra également de l'engagement d'autres acteurs. Sans aller plus loin, l'Armée elle-même devra s'adapter à une nouvelle façon de travailler, un processus qui se heurte toujours à des résistances au sein de toute organisation, mais qui est essentiel si l'on veut tirer le meilleur parti des nouveaux véhicules, qui sont très importants. loin d'être de simples assemblages mécaniques.
Pour l'instant, l'entreprise a déjà présenté son projet au Forum de Tolède, organisé par MALE. Dans les mois et années à venir, ils continueront à travailler, car ils considèrent qu'il s'agit d'un élément différenciateur par rapport à la concurrence et ils sont convaincus que la possibilité d'offrir un meilleur soutien au cycle de vie de leurs produits finira par faire pencher la balance dans les prochains concours. . S’ils tiennent toutes leurs promesses, nous sommes convaincus qu’ils le feront.
Soyez le premier à commenter